1. 板探:用来制造大口径埋弧焊直缝钢管的钢板进入生产线后,首先进行全板超声波检验;
1. Plate probe: after the steel plate used for manufacturing large diameter saw straight seam steel pipe enters the production line, the full plate ultrasonic inspection shall be carried out first;
2. 铣边:通过铣边机对钢板两边缘进行双面铣削,使之达到要求的板宽、板边平行度和坡口形状;
2. Edge milling: the two edges of the steel plate are milled on both sides by the edge milling machine to achieve the required plate width, plate edge parallelism and groove shape;
3. 预弯边:利用预弯机进行板边预弯,使板边具有符合要求的曲率;
3. Pre bending: pre bending machine is used to pre bend the plate edge, so that the plate edge has the required curvature;
4. 成型:在JCO成型机上首先将预弯后的钢板的一半经过多次步进冲压,压成"J"形,再将钢板的另一半同样弯曲,压成"C"形,形成开口的"O"形
4. Forming: on the JCO molding machine, the half of the pre bent steel plate is firstly pressed into "J" shape by multiple step stamping, and then the other half of the steel plate is also bent and pressed into "C" shape, and finally an open "O" shape is formed
5. 预焊:使成型后的直缝焊钢管合缝并采用气体保护焊(MAG)进行连续焊接;
5. Pre welding: weld the formed straight seam welded steel pipe and use gas shielded welding (MAG) for continuous welding;
6. 内焊:采用纵列多丝埋弧焊(更多可为四丝)在直缝钢管内侧进行焊接;
6. Internal welding: longitudinal multi wire submerged arc welding (up to four wires) is used to weld the inside of straight seam steel pipe;
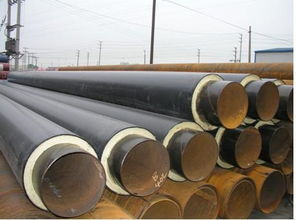
7. 外焊:采用纵列多丝埋弧焊在直缝埋弧焊钢管外侧进行焊接;
7. External welding: longitudinal multi wire submerged arc welding is used to weld the outside of LSAW steel pipe;
8. 超声波检验Ⅰ:对直缝焊钢管内外焊缝及焊缝两侧母材进行100%的检查;
8. Ultrasonic inspection I: 100% inspection of internal and external welds and base metal on both sides of longitudinal welded steel pipe;
9. X射线检查Ⅰ:对内外焊缝进行100%的X射线工业电视检查,采用图象处理系统以保证探伤的灵敏度;
9. X-ray inspection I: 100% X-ray industrial TV inspection shall be carried out for the internal and external welds, and the image processing system shall be used to ensure the sensitivity of flaw detection;
10. 扩径:对埋弧焊直缝钢管全长进行扩径以提高钢管的尺寸精度,并改善钢管内应力的分布状态;
10. Expanding: the full length of saw straight seam steel pipe is expanded to improve the dimensional accuracy of the pipe and improve the distribution of internal stress in the pipe;
11. 水压试验:在水压试验机上对扩径后的钢管进行逐根检验以保证钢管达到标准要求的试验压力,该机具有自动记录和储存功能;
11. Hydraulic test: the expanded steel pipes are inspected one by one on the hydraulic testing machine to ensure that the steel pipes meet the test pressure required by the standard. The machine has the function of automatic recording and storage;
12. 倒棱:将检验合格后的钢管进行管端加工,达到要求的管端坡口尺寸;
12. Chamfering: process the qualified steel pipe end to meet the required groove size;
13. 超声波检验Ⅱ:再次逐根进行超声波检验以检查直缝焊钢管在扩径、水压后可能产生的缺陷;
13. Ultrasonic inspection II: ultrasonic inspection shall be conducted one by one again to check the possible defects of longitudinal welded steel pipe after expanding and water pressure;
14. X射线检查Ⅱ:对扩径和水压试验后的钢管进行X射线工业电视检查和管端焊缝拍片;
14. X-ray inspection II: conduct X-ray industrial TV inspection on the steel pipe after expanding and hydrostatic test and film the weld seam at the pipe end;
15. 管端磁粉检验:进行此项检查以发现管端缺陷;
15. Magnetic particle inspection of pipe end: this inspection is carried out to find defects at pipe end;
16. 防腐和涂层:合格后的钢管根据用户要求进行防腐和涂层。
16. Anti corrosion and coating: the qualified steel pipe shall be anticorrosive and coated according to the requirements of users.